2020年11月以来,全市各级市场监管部门围绕降低企业成本、提高产品合格率、提升企业效益、重树企业管理理念等方面采取多项措施聚力破解小微企业质量管理中的难点、痛点、堵点,扎实开展小微企业质量管理体系认证提升行动。截至目前,全市共培训小微企业1000余家次,培训企业员工4000余人次,精准帮扶200余家企业,有效提升了企业质量管理水平,形成了胶合板和玩具行业质量管理核心过程实施指南,实施发布了胶合板行业质量管理体系实施规范团体标准—《胶合板生产企业质量管理体系实施规范》,促进了行业、产业和区域经济高质量发展。在提升行动中,涌现出一批可推广可复制的质量提升标杆,为发挥示范引领作用,市局从各县区推荐的160余个小微企业提升行动案例中,选取做法典型、成效突出的20个企业案例予以分享。
优良案例一
规范过程管理 促进质量提升
山东吉承装饰材料有限公司主要生产生态板、家具板、无醛板、普通胶合板、LVL胶合板、LVB胶合板等,拥有18条人造板生产线,年产人造板30000立方米。
经过深入排查,企业质量管理最突出的问题是过程控制不精细、不精准,产品的平均合格率为95%-96%,返修造成了工时和成本的增加,产品质量不稳定随之带来质量投诉问题。
公司针对上述问题,组织开展质量提升活动:制定质量方针目标,全员树立质量意识。树立经营理念,制定质量方针,确定质量目标,促使企业管理人员和一线工作人员对质量管理有了明确认识。加强人力资源培训,建立健全管理机构。对新上岗员工和特殊工种人员进行培训,并通过面视、实际操作等方式验证培训的有效性。选配素质高、专业能力强的人员组建质检队伍,成立专门的质量管理网络机构,搭建公司、车间、班组3级质量管理体系,实行一级抓一级,一级保一级、一级管一级的闭环式质量管理措施。实行精细化管理,建立全过程的质量管理模式。根据各车间生产工艺识别出完整的生产过程和关键工序,按照产品的生产过程逐项进行质量控制,实行进厂检验、过程检验和最终检验,实行质量标准考核制和质量“三检”制度,确保生产全过程可查可控。
通过贯标、认证和持续改进,实现了对人员、设备、原料、方法、环境等因素的科学化、规范化管理,产品一次合格率平均达到98%-99%,返修后二次合格率高于99%,产品质量稳定性有效提升,对比建立质量管理体系前,年顾客投诉量下降约50%。
优良案例二
引进智能装备 转型精益生产
山东安信木业有限公司是一家集国内外木制品产品设计、生产、定制、整装、贸易、配送、服务于一体的智能化家居制造企业。
通过深入剖析产业政策、消费者反馈意见、体系运行中不合格项反馈等情况,企业主要面临消费者对产品的绿色环保属性高需求以及定制过程把控不到位两大问题。
通过专家指导,企业针对定制家居新要求确定了智慧制造的发展路线:
1.打造智能模式,实现个性化定制新业态。自主研发安信美家AHC信息化管理系统,打通前端门店销售到中间工厂生产再到云端立体仓的智能传输全过程,运用3D设计远程信息管理系统,打造“标准+定制”的全屋快装模式,实现任意空间、任意款型与尺寸因需定制;通过互联网、大数据、云计算技术与工业生产4.0 标准智能基地结合,实现客户下单、智能设备自动化加工生产的全屋定制快装新家居服务模式。
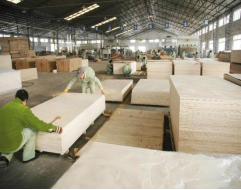

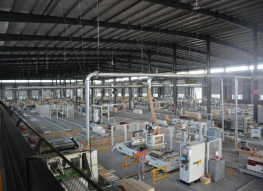
生产现场对比
2.打造无人仓储,实现产业智慧化管理。针对定制过程涉及物料多,人工容易出现漏发错发的问题,建设5500平米,高度达24米的自动化智能立体仓库,运用RGV自动化电脑穿梭车、提升机等智能设备,采用电子标签扫码识别方式进行出入库操控管理。利用WMS物联网仓库软件管理系统,使产成品通过系统管理从车间包装自动输送到达立体库指定货位,实现产业智慧化。

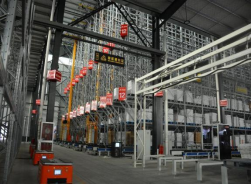
仓储现场对比
3.打造绿色产品,实现绿色环保生产新模式。实施绿色、环保、安全的产品生态体系,引进意大利进口水性漆涂装设备,使用环保涂装材料,做到低排放、低污染,有效解决甲醛、苯、重金属等有害物质超标的问题,大幅提升产品的绿色环保程度。
通过生产设备和技术的改造升级,采用高精准、智能化、绿色化的生产设备稳定了产品质量,减少了人工成本,提高了企业产能,目前企业的产品合格率达到100%,消费者满意率长期保持在99%以上;同时企业智慧制造的新模式颠覆了传统木工与传统定制体系,具有周期短、设计快、品质好、性价比高等特性,提高了公司的规模化、智能化生产水平,助力公司走上了品牌化道路。
优良案例三
强培训提质量 优环境严控制
山东广成塑业有限公司成立于2007年1月,是一家专业从事塑料集装袋生产的企业。
企业在人员质量意识,生产管理环节存在粗放式管理的弊端。
企业质量提升主要着力于提高人员质量意识及操作技能,改善现场环境,提升吨袋综合成品率,降低内外部质量损失。生产现场引入5S管理,通过交流研讨、绘制整理、整顿、安全草图,调整生产区域资源定置、布局;各个工序建立质量目标,设定质量管理目标和考核细则,从生产终端的成品率向生产始端逆推,控制方式前移至各主要工序过程,对各关键过程绩效参数的波动进行监控,从内外部成本损失入手,建立月度成本损失数据系统;制定实战化的培训计划,对岗位操作技能、设备使用、工艺规程、产品质量标准、监视记录填写进行培训,开展形式多样的练兵和操作比武,在实践中锻炼关键人员岗位操作技能;强化工艺过程控制执行,明确各过程的工序参数、产品特性指标控制界限和放行准则,加强工艺执行监督,强化各工序工艺控制,提高成品合格率及产品质量。
该企业通过质量提升行动,生产现场焕然一新,减少了人、物品的流转时间,生产效率得到显著提升,降低了物料消耗;
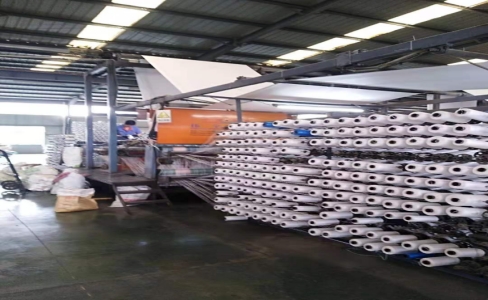
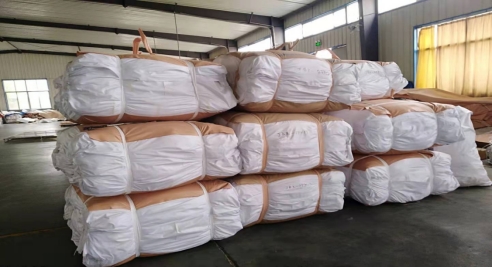
各岗位人员的操作技能有了不同程度的提高,投入产出率由92.5%上升到94.6%,一次合格率由87%上升到91%,设备故障率由3.6%下降到2.2%,工艺执行符合由98%上升到99%。
各工序的内外部质量损失有较大降低,“外部成本损失”方面,降幅明显,损失金额趋向于零,质量成本得到有效控制。
优良案例四
严控基础管理 自主创新生产
临沂开元轴承有限公司是专业生产圆锥滚子轴承的企业,主要生产销售轴承、轮毂单元、轴承专用设备等自产产品。
企业以往产品质量依靠“人员技能”和“个人经验”,部分生产工序产品尺寸偏差离散大,没有形成在线检测,造成人员成本过高和人员劳动强度大。
开展提升行动以来,公司从推行全过程标准化质量管理模式入手,以技术提升为支点,自主创新生产,着力做精做强轴承品牌。
1.从基础管理入手,全面落实质量管理制度。对原材料采购、产品生产和过程检验等环节严格按标准要求进行控制,严格按工艺文件要求组织生产,加强对车间工艺执行情况和仓库成品、半成品存放情况的监督检查,
2.重视自主知识产权和自主创新生产。加快推动新旧动能转换和质量提升,在做精做强轴承品牌的前提下,着手轴承精加工设备的设计和制造
3.加大设备投资,实现装备智能化、自动化。大幅度节约人力,减少装配过程中的磕碰、保证清洁度;以严格的生产过程控制、轴承技术提升和整体设计获取客户欢迎。
通过公司质量提升,建成轴承单元智能制造生产示范线,居轴承行业领先水平,轴承单元产品重量较原设计减轻10%左右,高端轴承及轴承单元市场占有率10%可增加到30%以上,已成为中国商用车第一品牌,得到陕汽、一汽、安凯等客户的认可。
优良案例五
持续改进提升 强化质量管控
山东帅克宠物用品有限公司是专业研制、加工、生产和销售宠物食品的高新技术企业。
公司在质量管理建设过程中还存在一定的不足,质量标准化建设还需进一步规范,产品检验过程、关键业务流程管理方面还需要进一步强化。
提升行动开展以来,公司采取了以下做法:
1.明确关键工作过程,形成质量管理机制。根据产品工艺特点、技术路线、战略目标和客户的需求变化,制定了公司的质量管理的关键过程:对产品过程进行准确识别,形成制度文件及管理机制,对产品质量过程进行管理。
2.引进绩效管理体系,推行质量过程管理。形成“公司至车间、车间至班组、班组至个人”层层考评的立体化、多层次的企业质量生产管理体系,实现公司质量管理体系的规范化、科学化、严格化、长期化。
3.建立三位一体的改进机制,不断进行有效改进。以绩效管理体系为框架建立改进目标、改进模式和改进方法三位一体的改进机制,以关键质量、关键工序和关键设备,售后服务反馈等为出发点,组织实施和改进,不断进行有效改进和质量提升。
4.引入信息化可追溯体系建设,进行质量管控。将宠物食品从原料进厂、生产加工、成品检验、入库发货等全过程进行质量管控,建立全供应链的质量安全信息系统,实现全面布控,加强对宠物食品售前、售中和售后的跟进服务。
通过质量提升行动,全面打通销售管理、生产管理、采购管理、仓储管理、财务管理等关键流程节点,提升了各部门之间的业务协同效率,全过程质量管控以“质”取胜,客户满意度情况良好,2022年销售额比去年同期增长60%。